Centrifugal Air Compressor DAC 50-900
...
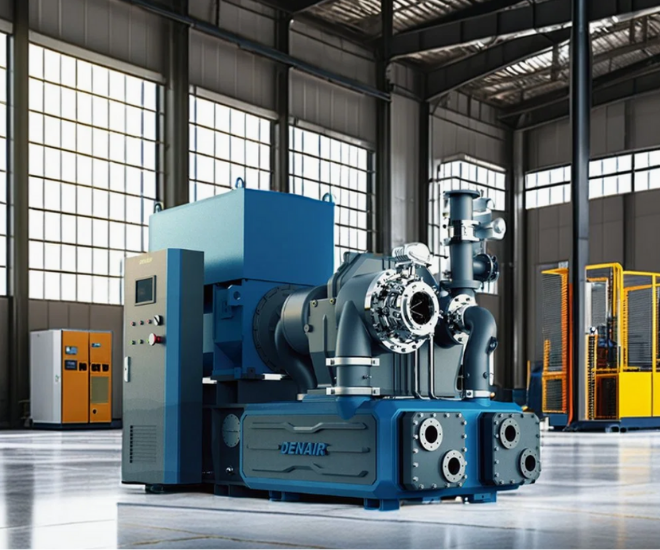
Centrifugal Air Compressor DAC 50-900
Working Pressure: 0.3-25 bar, 4-363 psig
Free Air Delivery: 882.75-105930 cfm, 25-3000 m3/min
Working Power: 132-14500 kW, 175-20000 hp
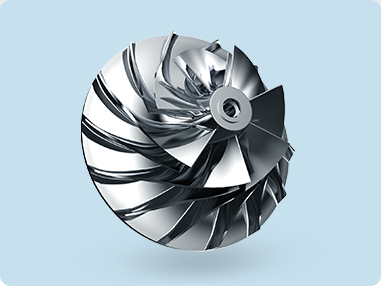
Impeller:
The aerodynamic design of Denair centrifugal compressors applies advanced aerodynamic principles, combined with self-developed high-efficiency modeling software, CFD simulation and other means, to ensure optimal inter-stage compression ratio distribution and stable reliability; The long-term product verification design experience, rich impeller database and design software of Denair team ensure the superiority of aerodynamic design.
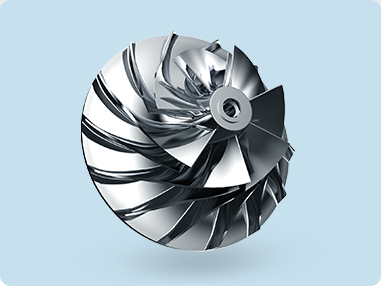
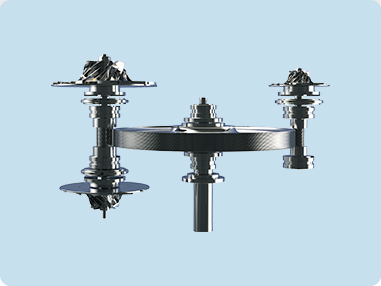
Rotor Dynamic Design:
Professionally designed rotors and bearings ensure that they can operate under reasonable oil film temperature, pressure and thickness, effectively reducing bearing power consumption. Through extracting the stiffness and damping data from a large number of bearings, DENAIR conduct rotor dynamics analysis to ensure reasonable vibration value of the rotor as well as ensuring the rated speed setting is far away from the critical speed and enhancing the stability of the whole machine.
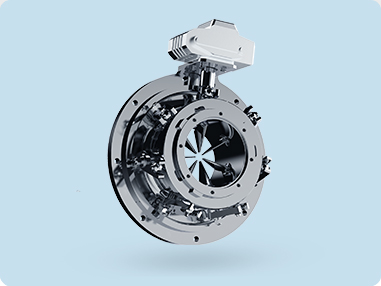
High Performance IGV:
The electric actuator drives the airfoil stainless steel blades, precisely controls the opening of the inlet guide vanes, changes the pre-swirl value of the intake air, and improves the operating efficiency of the centrifugal compressor. When the compressed air demand is reduced, the IGV can save up to about 9% energy consumption, making the centrifugal compressor run efficiently and energy-saving.a
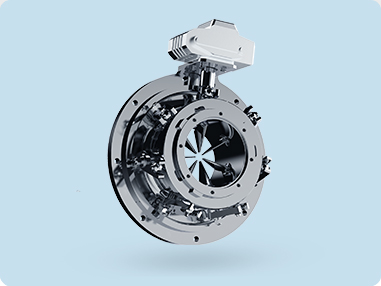
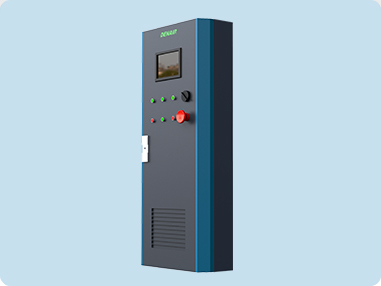
Control Cabinet
The highly integrated control cabinet adopts Siemens PLC with touch display screen, which is concise and clear and easy-to-operate. Our controller supports multi-languages switching and all parameters read and displayed in real time, especially key information like running curves and numbers. Meanwhile, automatic alarm, chain shutdown protection, anti-surge and surge prediction fuction are available to ensure the safety and reliability of equipment operation.
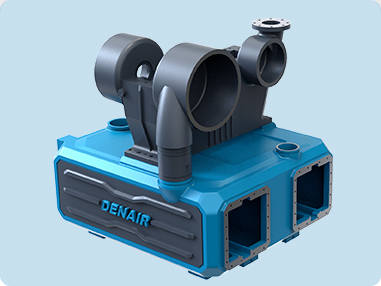
Integrated Casting Gearbox
Adopting modular design, the horizontally split gearbox is integrally cast with volutes at all stages while the cooler box is integrally cast design. Compared with the splitted and welded gearbox, compression unit of horizontal one is with higher strength mechanism, fewer processing surfaces, more reliable operation and there is no assembly error, no deformation, low noise and low vibration between the volute and the gear box at all stages. Compared with integral casting, processing, assembly, transportation, on-site installation and maintenance f or our coolers are simpler. When compression unit needs to be returned to the factory for overhaul, the integral casting requires larger lifting equipment and destroys the installation foundation, resulting in secondary installation but ours, which is modular design, perfectly solve this problem.
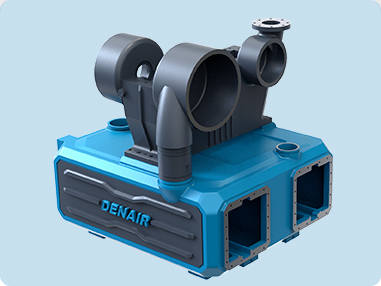
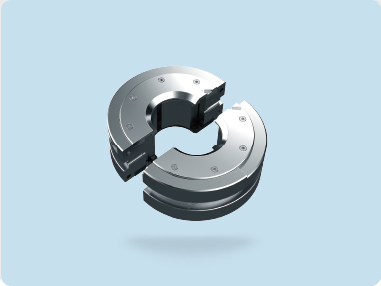
High Reliability Bearing
Through the professional design of rotor dynamics, the tilting pad bearing with high load capacity and low vibration is adopted. The bearing bush can be automatically adjusted according to the load and temperature changes, so as to ensure the stable operation of the unit under various harsh working conditions.
High-Performance Machines Profitable Solutions